Top 7 tips for getting an ERP Software Selection on Track
You’re looking to find out how to get an ERP Software Selection back on track. This means that you probably have an evaluation that is going poorly and you are being led by the ERP software vendors, right? The ERP Software Selection process can be a struggle, but they don’t really have to be. If the ERP Software Selection follows a clear process, then things will run smoother. The trick is to not let the software vendors drive ERP Software Selection process.
Key ERP Software Selection Tips
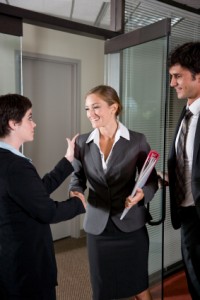
1. Get Senior Management on board now
2. Be sure you have clear goals
3. Define your both your technical requirements and business requirements
4. Have a neutral third party manage the process.
5. Eliminate vendors early, and without regrets
6. Be sure you are working with the right software providers
7. Reassess your internal team
One of the top things you can do to ensure success of any Enterprise Software Selection project is to ensure that senior management is on-board with the project and that they fully support the goals of the project. If top-line management is not supportive of the project, there will be departmental and division contentions during the implementation. Often these arise during the selection process. Usually it is the case of one department competing for the same resources as another department. This often will show up on conflicting requirements for the system. Senior management must be the tie-breaker and define the future path the system should take.
If the project does not have clear goals, it is bound to flounder. Goals should not be general such as replace our system by next January. The goals should have significant business impact. A goal like “Reducing inventory by 25% while increasing sales throughput by 15% one year after implementation” is a clear goal that benefits the business and lays a stake in the ground that the system must achieve. You may find that the system can help you exceed that goal, but if you do not measure in a clear goal such as this, how will you know you have succeeded? The pain and inconvenience of an implementation will create a lot of problems within the company, but a clear goal is a great focus agent to get past the disagreements and personality conflicts.
ERP Software Selection Requirements
Often a company will define a set of requirements for a system and these requirements will have no impact on the decision of the system. Requirements need to be business driven and be tied to the factors that make your company successful. Look at the following two requirements and see which one makes it easier to help in a selection:
1. System must have serial and lot tracking.
2. System must be able to report on all shipments by a particular lot with traceability back to the original batch or incoming receiving document.
These two statements are essentially asking for the same thing, but when it comes time to solve a problem, the second requirement will distinguish of the system can solve the problem. Define your requirements around business processes, not about system features.
Additionally, most systems nowadays can handle most of the key things you need. They all do General Ledger, Accounts Receivable, Inventory, etc. The question is, what are their strengths and what are their weaknesses. Defining specific business process requirements around the things that you do frequently is the best way to ensure that you get a system that matches your needs.
Many times when companies get in trouble with an ERP Software Selection, it is because they tried to manage it on their own. Often the IT manager or even the Controller will get the task of defining requirements and shepherding the system selection and all the vendors, value-added-resellers, and reference clients. Since they already have a key role in the company, it often a daunting task to get them to manage the selection process and do their day job. Because of this, it is often advisable to get a third party consultant involved to manage the process. The key thing about this consultant is that they should not have any financial ties to any vendors. They need to be non-biased and have experience in many ERP Software Selection projects.
Why does this help? There are a few reasons, but the key reason is that they can supplement your time and handle all of the details around gathering requirements, building scripts, arranging demos, and being the one to have to tell the vendors “no” at the end. Further, they usually come with a broader vision of how the end result can be achieved. They also make a living out of doing these selections and they know the pitfalls and can help you avoid many of the vendor “tricks” that are often played to ensure that the salesperson wins the sale. If your selection is already off track, bringing in a consultant can often help realign the various team members and refocus the selection.
As you move into the ERP Software Selection process, it is important that you eliminate as many potential candidate software systems early on, so you are not wasting your time and efforts looking at a broad range of systems. Ideally, you start with a long list of 10 and whittle that down to the top two or three. Get the software vendors that are clearly not matching your requirements out of the running as soon as possible. Use resources to help you define the best fit for your company. Many times, the vendor will bow out if they see they are not a clear fit to your requirements. But with each elimination, document why they were eliminated, so that at the end, when someone asks, “What happened to XYZ software, I thought they were a good fit”, you will have the answer as to why they are no longer being considered.
Once you have chosen the two or three candidate software systems, you want to make sure that you are working with the right provider. Software is sold either direct or through indirect channel partners. The channel partners, or value-added-resellers (VARs) each come with their own specialties. You need to find out are you dealing with a VAR or with the Software company itself. If you are dealing with a VAR, you need to make sure that they are the best VAR to help you implement the software. Do your research early, because the last thing you want to do is to change VARs late in the process. This causes all sorts of problems, most of all it delays the selection by weeks or months.
When dealing with VARs, talk to the Software Developer (see our directory of ERP software vendors here) and get their take on the VARs strengths and weaknesses and see if there may be another company you can speak with. Interview the two implementers (VARs) and see which company is a best fit to work with your company. Often it comes down to personality, one group was too arrogant, one group just didn’t get us, or even that VAR’s sales rep had a horrible personality. Find the fit because if you select their ERP software, you will be living with these people for 6-9 months or more. You want to make sure that you can work through the implementation with them as well as later rely on them for ongoing support.
If you are dealing with the software company direct, the same questions apply, but in a sense of is this the software to get married to? You need to be sure that not only the software works for you, but also that the people and company are a good fit to work with your company.
Lastly, take a good, hard look at your team. Do you have functional members from each department? Do they each bring a wealth of experience about their area? Often the hardest thing about the ERP Software Selection process is getting the best people in your company and pulling them out of their jobs to take part in the critical task of selecting a new system. They are usually the person most in demand. They need to be the one to help select the system as they know the current system and business processes inside-out.
Often an ERP Software Selection will go badly because the best people can’t give the time to make the process happen. This is why it is so important to have senior management involved and have a clearly stated set of goals for the project. Having a third party to help move things along and to look at your business objectively will aid tremendously in making the ERP selection process easier. Most of all, by putting all seven of these tips together, you will ensure that you have a successful ERP Software Selection process and that you end up with the best software for the success of your company.
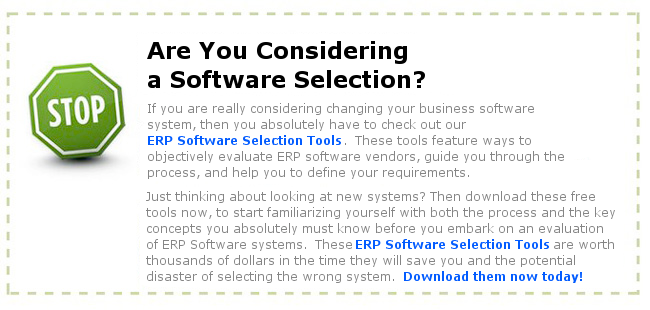
ERP Software Selection